If your Company supplies or provides an innovative product or services you can tell the shipping community about. Or if you have a Case Study you can share with the industry professionals and your potential clients here. Just send the information to info @ seavendors.com with title ARTICLE. Any questions? Contact us.
Wire ropes are largely used in marine environment or for rigging purposes. They receive considerable loads and thus suffer a great deal of mechanical damage throughout their service life. Moreover, research has shown that the major cause of wire rope failure is excessive deterioration and corrosion, lack of maintenance and inspection, and wrong usage resulting in early discarding, reduced safety and replacement cost increase.
Sometimes damage can be easily detected, while in other cases fractured wires may occur on the inside. Hence, wire ropes should be inspected and maintained by the right person (competent person assigned by the company), to assure they’re in perfect condition. Regular inspections ensure high rope performance, long service lifetime , safety of personnel and equipment, and reduced operating costs.
In this article we will be describing ways to perform a wire rope inspection and we will provide solutions for meticulous maintenance.
- How often should ropes be inspected?
- How do you calculate wire rope strength?
- How are wire ropes classified?
- How to perform a visual wire rope inspection
- Wire rope maintenance
- Wire ropes by Katradis
HOW OFTEN SHOULD ROPES BE INSPECTED?
All ropes (synthetic, high modulus and wire ropes) should be inspected before and after an operation. This guideline ensures maximum safety for both a ship’s personnel and equipment. Even though it’s difficult to determine the exact service life span of ropes, there is a way to have a more precise estimation about their efficient lifecycle. Calculating the exact time ropes have been in use (e.g mooring time, mooring conditions, weather and tidal conditions) is the answer. All in all, rope inspections should occur at least once a year.
Inspecting wire ropes in particular, comes with great responsibility. Inspection results should be recorded, and any defects noticed have to be reported and addressed properly. Some defects can be repaired, while in some cases replacing a wire rope is inevitable.
Periodical inspections of vessel deck equipment is also crucial for maintaining the good condition of wire ropes. The condition of the drum, chocks, bitts, rollers, sheaves, cable clamps and other end fittings, affect the rope’s performance, threads and cords. Make sure to mark these parts during your overall inspection.
In order to help marine officers and staff conduct successful wire rope inspections – and keep an up-to-date record of them – we have created an inspection solution that helps in maintaining and monitoring a ship’s ropes and deck equipment.Learn more about Katradis inspection Neptune Solution
HOW DO YOU CALCULATE WIRE ROPE STRENGTH?
The Maximum Safe Mass of a wire rope can be calculated using Newton’s second law:
m = F / g
where F = force (N), m = mass (kg) and g = acceleration of gravity (9.81 m/s2).
When calculating mass using F = Minimum Breaking Force, according to the wire rope’s diameter, you can determine the Minimum Breaking Mass and therefore the wire’s max strength. When calculating mass using F = Safe Load according to the wire rope’s diameter, you can determine the Safe Load Mass, which is the advised load for this rope diameter.
Table I: Wire rope strength calculation variables
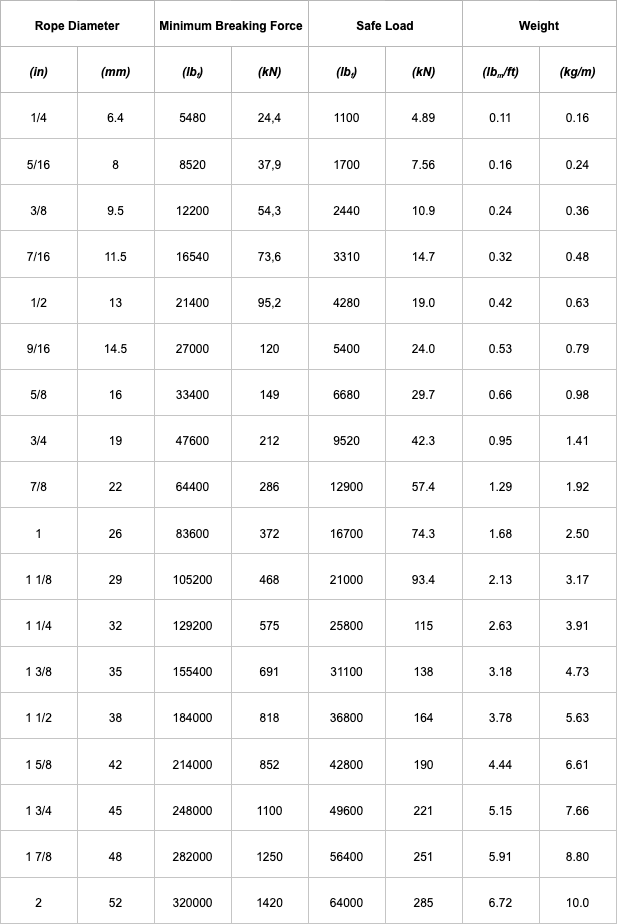
The strands of a wire rope absorb the majority of the tensile force applied on the rope. Their design and manufacturing standards affect the level of fatigue resistance and resistance to abrasion. An easy way to understand which rope design is suitable for each purpose, is the wire rope classification.
HOW ARE WIRE ROPES CLASSIFIED?
Wire ropes are classified according to the number of strands in each construction and the number of wires in each strand. For example, a classification of 6X19 means that a wire rope of this type always has six strands, but its wires could be 15-26 per strand. This is because 19 is not the exact number of wires, but the classification of a wire number range.
HOW TO PERFORM A VISUAL WIRE ROPE INSPECTION
Visual inspections are a common and fast way to assess wire rope condition. Both the standard and rotation resistant wire rope inspection process comply with the same four steps of examination. A ship’s crew can perform them as follows:
Step 1:Visual inspection for distortion
Steel wire rope distortion is obvious in most cases and can easily be identified by the inspector or the ship‘s crew. It usually occurs if load is suddenly applied or abruptly released (shock loading), or even if swift torque is forcefully induced.
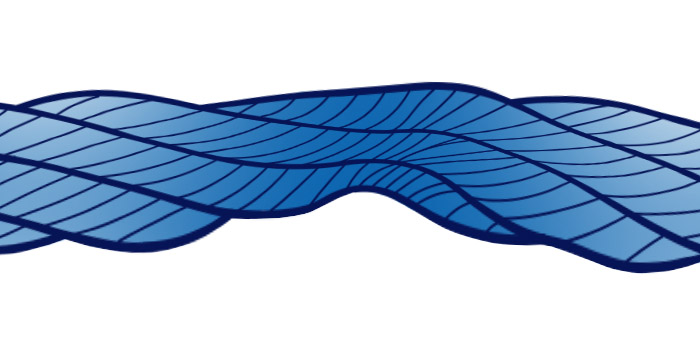
Usual types of wire rope deformation are:
- Wave distortion
- Bird-caging
- Core rope displacement or fracture
- Kinking (that can develop in “dog-leg” deformation)
- Swelling / constriction (localized
Although not all of these deformations make the rope absolutely dangerous to use, they all may cause ropes to wear unevenly in time. This means inspections should take place more often, and distorted ropes should be handled with caution.
By any means, replacing a heavily distorted steel wire rope is a necessity.View rotation resistant wire ropes
Step 2: Cloth rag testing – Rag and visual
The rag and visual inspection is a good method for regular inspection intervals. The inspector pulls a rag along the rope trying to find broken wire cords. If the rug gets snagged by the rope, the inspector has to stop and assess the wire rope’s condition. Extreme caution should be exercised during the visual inspection, and under no circumstances should this method be the only one used to inspect wire ropes.
Tip: When you encounter a protruding wire end, bend it back and forth manually, until it separates from the wire. This will protect neighboring wires from wearing out.
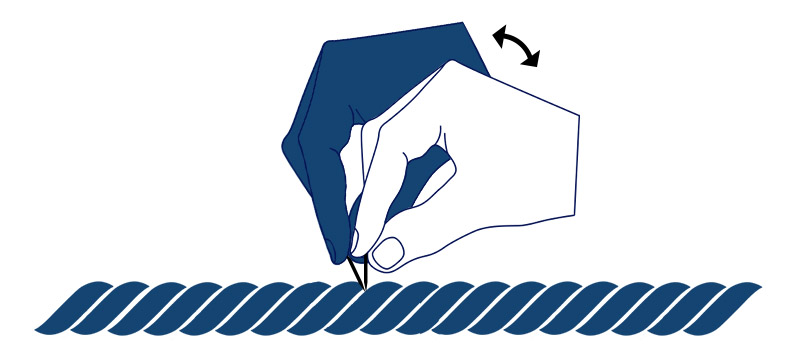
Step 3 – Wire rope diameter calculation
Diameter reduction is a critical factor in steel wire rope wear and if not properly taken care of, it can result in rope breakage. Excessive abrasion, loss of core mass, corrosion or inner wire failure are all factors that contribute to diameter reduction.

To get an accurate measurement of the rope’s diameter, measure the rope at three different points at least 5 feet apart. Take the average of these three measurements to determine the true diameter.
Any measurements showing a reduction of ⅓ or more, indicate that a replacement should follow without delay. A diameter reduction of less than 1/3 still requires attention, and the inspector or the ship’s crew should be on guard in the next scheduled wire rope inspection.
Step 4 – Abrasion, corrosion, pitting & deep lubrication check
Failure from abrasion or corrosion is a result of deficient deck equipment inspection or insufficient wire rope lubrication respectively. Internal corrosive damage is more difficult to identify than any other types of degradation. In most cases, the damage has progressed more than the external signs suggest.
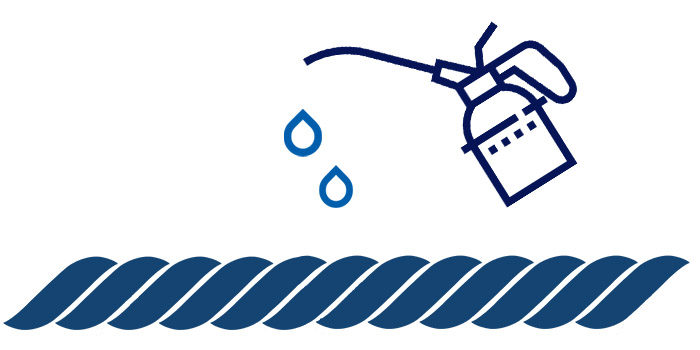
During a corrosion focused inspection, three damage stages may appear:
- After cleaning there isn’t any corrosion to be detected. – No action needed.
- There are signs of surface oxidation and the wire rope is rough to touch. – Clean, lubricate and inspect the rope regularly.
- There are slack wires and heavy pitting that may lead to rope breakage. – Remove the rope from service immediately.
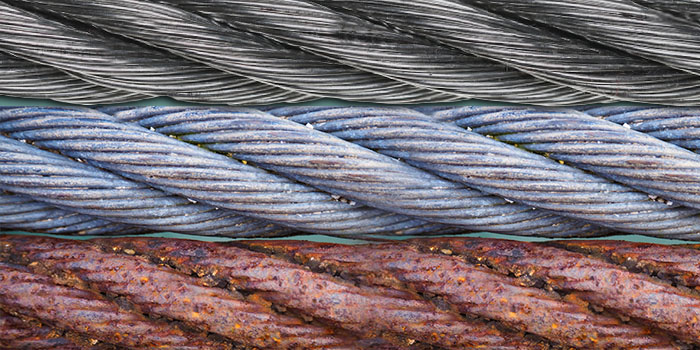
WIRE ROPE MAINTENANCE
Storage
Wire rope storage plays a significant role in the rope’s operation life. Wire rope corrosion and pitting can be avoided if ropes are safely stored in a clean, cool, dry and well-ventilated place. Steel wire ropes should not by any means rest on the floor, and should be protected from water, dust or any chemical fumes. Long term storage requires periodic greasing, turning the reel upside down for preventing grease dripping and possibly re-winding to another reel with larger inner tube diameter.
Lubrication
Wire ropes should be maintained with periodical lubrication. In order to prevent internal corrosion, a pressure lubricator is suggested to be used. In this case, a small amount of grease is used to lubricate the rope internally, while the deck stays grease-clean. Pressure lubricators clean the rope before they grease it so that the new grease enters a clean rope. The type of grease used is very important for maximum protection and greasing efficiency.
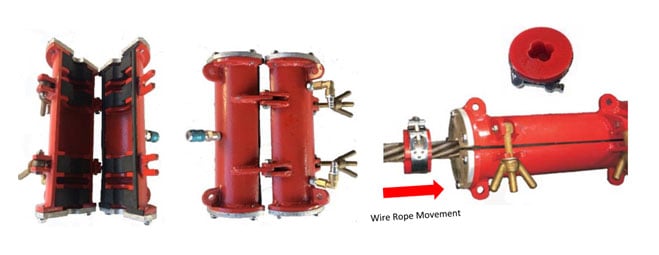
Learn more about the Pressure Lubricator
Cleaning
Steel wire ropes exposed to dirt, grime and other contaminants, have to be cleaned with a wire brush and petroleum (unless a pressure lubricator is used). Optimal cleaning of wire ropes can extend their service life and guarantee safe operations.
Reeling
The reeling process is of high importance for the longevity of wire ropes. To protect them from being damaged, it is important that the surface of the drum is clean, smooth and dry. Improper reeling may cause wire-rope strands to spread or get flattened, when in contact with one another, as successive layers are being spooled and upper layers apply pressure on the lower ones.
WIRE ROPES BY KATRADIS
Katradis S.A. offers a wide range of top quality wire ropes for shipping (mooring and hoisting operations), fishing and construction purposes. Our wire ropes have greater resistance to fatigue, and they distribute tension force equally among the rope strands. They are less likely to kink, providing higher staff safety and assuring operation success.Choose your new wire ropes
Source: KATRADIS MARINE ROPES IND. S.A.